top of page
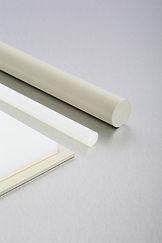
Polypropylene Sheet
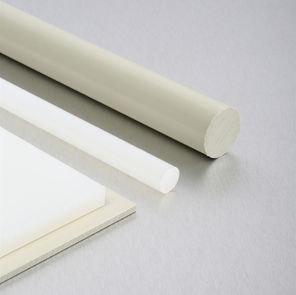

Polypropylene Sheet
Polypropylene Homopolymer
PPH is a lightweight material with SG 0.91, offering excellent chemical resistance and stiffness. With a higher working temperature than PPC (0°C to +100°C), it retains low water absorption and is easily weldable. Compliant with food safety regulations, PPH is ideal for diverse applications, including the medical and food industries.
Properties
-
Excellent weldability
-
Excellent chemical resistance
-
High corrosion resistance
-
High rigidity in upper temperature range
-
Higher working temperature than PPC
-
Food compliant
Applications
-
Chemical tanks
-
Water applications
-
Medical
-
Equipment construction
-
What are the characteristics of Nylon 6 Sheet?Nylon 6 Sheet is recognized for its strength and flexibility. It can absorb shock and vibration effectively, making it an excellent choice for impact and shock resistance. In applications requiring high wear and friction resistance, Nylon 6 Sheet outperforms many materials like Bronze or Brass, offering longevity with minimal maintenance. Moreover, Nylon 6 Sheet is often praised for reducing noise during operation, especially in Nylon gears, which not only last longer but also act as sacrificial components to prevent costly damage in case of catastrophic failures.
-
What is Cast Nylon 6 Sheet?The other manufacturing process for Nylon 6 Sheet involves casting the polymer into a sheet mould. Although there may be slightly greater thickness tolerance and a slight chance of blow holes if not perfectly executed, cast Nylon 6 Sheet benefits from less stress due to the process, resulting in a more stable component. It is reportedly easier to machine and is the only option for thicker Nylon 6 Sheets.
-
What is Extruded Nylon 6 Sheet?Nylon 6 Sheet is manufactured using two different processes. Extruded Nylon 6 Sheet is produced by forcing the material through a die, resulting in a more accurate thickness and a cost-effective solution for thin sheets. While it may have slightly more internal stress and be a bit more challenging to machine due to easy melting during machining, it remains an excellent choice.
-
What is Nylon 6 Sheet?Nylon 6 Sheet is widely regarded as the most popular engineering plastic sheet due to its numerous advantages. While there are plastics that may outperform Nylon 6 Sheet in specific areas, its overall versatility makes it a winning choice for various applications. When considering materials for wear blocks, jigs, or fixtures, Nylon 6 Sheet is often the first choice. It is readily available in a wide range of sizes, including thicknesses of up to 100mm, with the possibility of custom fabrication for thicker requirements. Machining Nylon 6 Sheet is relatively easy when using appropriate tools like sharp and well-shaped smoothing cutters with coolant.
-
Is machining both faces of Nylon 6 Sheet necessary?When reducing the thickness of Nylon 6 Sheet through skimming, it's crucial to take an equal skim off both faces to avoid unevenly released stresses that could lead to an uneven and non-flat sheet. Drilling, tapping, and boring Nylon 6 Sheet are relatively straightforward with sharp tools, but it is essential to control heat buildup, as excessive heat during machining can result in a subpar surface finish.
-
What are the disadvantages of Nylon 6.6 Sheet?The main drawback of Nylon 6.6 Sheet lies in its price, as it is generally slightly more expensive due to the higher cost of the polymer itself. Additionally, Nylon 6.6 Sheet has a smaller size range and availability, particularly for mid-thicknesses and thicker options. The maximum thickness for Nylon 6.6 Sheet is around 100mm, and if thicker sheets are required, Nylon 6 Sheet should be considered.
-
How is Nylon 6.6 Sheet made?All Nylon 6.6 Sheets are manufactured through an extrusion process, where the polymer is heated and extruded through a die. While the extrusion process ensures relatively accurate thickness and surface finish, it can take longer than casting. Some stresses may exist within the sheet due to extrusion, but proper annealing and normalising processes reduce these stresses to a minimum. When reducing the thickness of Nylon Sheet, it is essential to machine off equal quantities from both faces to prevent distortion due to uneven stresses.
-
What is the difference between Nylon 6.6 and Nylon 6 Sheet?When choosing between Nylon 6.6 Sheet and Nylon 6 Sheet, it's essential to understand that Nylon 6.6 offers a slight advantage in various aspects.
-
Has Nylon 6.6 sheet got FDA approval?Natural Nylon 6.6 Sheet has received FDA approval, making it suitable for certain applications where food is produced. However, this approval does not extend to black Nylon 6.6 Sheet, which contains additives that render it unsuitable for food contact.
-
Does Nylon 6.6 Sheet have a higher operating temperature?Yes, Nylon 6.6 Sheet boasts a slightly higher operating temperature, making it a suitable option for applications requiring an extra safety margin or when operating at the edge of the temperature range for Nylon 6 Sheet.
-
Is Nylon 66 Sheet a little bit harder?Indeed, Nylon 6.6 Sheet is slightly harder than Nylon 6 Sheet, contributing to its low friction properties, providing a slippery surface. This increased hardness also enhances its machinability, further supported by the improved temperature range, reducing the risk of melting during machining.
-
Is Oilon Sheet highly rated?Oilon Sheet has consistently lived up to its reputation, impressing customers during real-life trials and service in harsh and abrasive environments. Its exceptional performance has convinced numerous customers to switch from regular Nylon Sheet to Oilon Sheet. Additionally, Oilon Sheet makes slide blocks much quieter in operation, which has become an unexpected and valuable selling feature.
-
What is Oilon Sheet?Oilon Sheet and block represent a significant performance upgrade compared to natural Nylon 6 and even the black grade. Although Oilon Sheet is essentially Nylon 6, its exceptional qualities stem from a special additive mixed in during the early stages of manufacturing. The key to Oilon Sheet lies in an industrial-grade oil lubricant blended into the material, ensuring a perfectly even distribution throughout the entire structure of the sheet.
-
Is Oilon Sheet easy to machine?Oilon Sheet machines similarly to regular Cast Nylon, with the added advantage of the extra lubricant providing some benefits in machining. It is manufactured using the cast process, resulting in an engineering plastic with lower stress levels. Rigorous annealing processes reduce internal stress to a minimum, ensuring that machined components remain stable after the machining process. The size range for Oilon Sheet is considerable, and even special sizes can be sourced within a few weeks from the factory. With extensive experience in Oilon and all engineering plastics, Direct Plastics maintains substantial Oilon Sheet stock for immediate delivery from its warehouse in Sheffield.
-
What colour is Oilon Sheet?Oilon Sheet is easily recognizable by its green colour, with the shade varying from batch to batch, often resembling British Racing Green.
-
HDPE Sheets: Why should you use them?With its almost waxy texture, HDPE Sheet is an excellent material for low-friction wear strips, commonly utilised on conveyors and production lines in large companies. Its outstanding wear resistance and low friction properties make it a preferred choice in this environment. However, bonding HDPE Sheet to other materials can be challenging, often requiring mechanical fixation using screws or similar methods. HDPE Sheet is well-suited for machining on CNC or traditional machines, resulting in a smooth surface finish.
-
HDPE Sheet has some drawbacks. What are they?HDPE Sheet may not be suitable for applications requiring high impact resistance from heavy objects, as it is slightly softer than some other engineering plastics like Nylon or Acetal. The material may exhibit marks if pressed with strong force, although this attribute can be advantageous in certain scenarios, such as in canning factories, where it causes no damage to cans.
-
HDPE Sheet: How does it look?300 grade HDPE Sheet often has a glossy and a matte side. Like most engineering plastics, HDPE Sheet lacks a protective coating, making it more suitable for industrial or engineering applications where a perfectly scratch-free surface is not essential.
-
How does HDPE Sheet work?HDPE Sheet, also known as High Density Polyethylene Sheet, is a highly versatile engineering plastic widely recognized as "chopping board material," commonly used in food production facilities and domestic kitchens. Its knife-friendly surface ensures longer blade sharpness, and its food-safe properties make it the preferred plastic for food-related applications. HDPE Sheet is generally available in two grades: HDPE 300 and HDPE 500, with the numbers indicating the density of the plastic. HDPE 500, being the denser and slightly harder grade, comes at a slightly higher cost.
-
What is the summary of HDPE Sheet?HDPE Sheet is an economical, abrasion-resistant, and low-friction engineering plastic, making it a great choice for various applications. For high load or impact resistance or materials that bond easily, Nylon Sheet may be worth considering. For any assistance, please contact our technical team at Direct Plastics, where we maintain a vast stock of engineering plastics, including HDPE Sheet, for immediate delivery from our warehouse.
-
What are the applications of Polypropylene Sheet?Polypropylene Sheet finds use in a variety of applications, such as acid and chemical tanks, industrial chopping boards, certain cladding applications, and even prosthetic components.
-
What are the two types of Polypropylene Sheet?Polypropylene Sheet is available in two types: Copolymer and Homo-polymer. Co-polymer contains HDPE for increased flexibility and impact resistance, while Homo-polymer is pure Polypropylene.
-
What are the drawbacks of Polypropylene Sheet?Polypropylene Sheet has a few considerations to keep in mind. Its low melting point makes it more challenging to machine, requiring care to avoid excessive heat generation. Bonding Polypropylene Sheet can be problematic, often requiring specialised processes like plastic welding. Its fire resistance is poor, with a HB fire rating, making it unsuitable for certain cladding applications. The availability of colours is limited in the Homo-polymer grade, which is only available in natural and beige. However, Co-polymer grade Polypropylene Sheet comes in various colours to suit different needs.
-
What are the benefits of Polypropylene Sheet?Polypropylene Sheet offers excellent acid and chemical resistance, including resistance to Sulphuric Acid. Its affordability is a significant advantage as it is one of the most cost-effective engineering plastics. Polypropylene Sheet also provides high impact resistance, making it suitable for backing boards in various applications. Moreover, it is remarkably lightweight and has the unique property of floating.
-
Does PTFE Sheet have a famous trade name?PTFE is also referred to as Teflon® (DuPont).
-
Is there a summary for PTFE Sheet?PTFE, famously known as Teflon®, is a highly chemically resistant plastic with remarkable properties. Its exceptional thermal stability and low coefficient of friction make it an excellent choice for various applications. Though challenging to machine and bond, PTFE's unique characteristics and versatility make it a valuable material in different industries.
-
What is the size range, colours, and availability of PTFE Sheet?PTFE Sheet is available in white (natural) and comes in thicknesses ranging from 0.5mm up to 50mm.
-
What are the drawbacks of PTFE Sheet?While PTFE Sheet is a versatile material, it does have a few limitations to consider. It has minimal "plastic memory" and may be subject to creep. To limit this effect, a version of PTFE with fillers must be used. PTFE is described as soft, which can lead to damage or distortion when clamped. It is not considered tough and lacks high tensile strength. Additionally, PTFE decomposes above 350°C, producing lethal fumes to birds and flu-like symptoms in humans.
-
How does PTFE Sheet compare in terms of wear resistance?PTFE Sheet wear resistance depends on factors such as the roughness of the opposing material, speed, and load applied. For high-wear applications, other engineering plastics like UHMWPE may be a better choice.
-
What benefits does PTFE Sheet offer?PTFE Sheet boasts several advantages that make it a preferred choice for various applications. It exhibits an incredibly low coefficient of friction, making it ideal for high-temperature and low-friction uses. Additionally, PTFE's excellent dielectric properties make it suitable for microwave frequencies in printed circuit boards. It is one of the most thermally stable plastic materials, withstanding temperatures up to 260°C without appreciable decomposition. Moreover, PTFE serves as a high-performance substitute for polyethylene in low-cost applications, owing to its higher melting temperature.
-
Can PTFE Sheet be used in food applications?Yes, PTFE is famously known for its use in DuPont's Teflon® lining for cookware, making it suitable for food-grade applications.
-
Why should you choose PTFE Sheet?PTFE Sheet offers exceptional advantages, including super low friction, high chemical resistance, low and high-temperature capability, weathering resistance, and excellent electrical and thermal insulation.
-
Can PTFE Sheet be glued or bonded?PTFE Sheet requires surface preparation prior to bonding, such as etching with a solution of sodium and naphthalene in tetrahydrofuran. Adhesive manufacturers offer proprietary primers that prepare the surface for adhesive bonding. Various adhesives, including epoxies, polyurethanes, and acrylics, can be used. Special acrylic-based adhesives from companies like Loctite® and 3M® can bond directly to PTFE without extensive pre-treatment.
-
What should be considered when using PTFE Sheet?PTFE Sheet can be hazardous when heated above 400°C, releasing toxic emissions. Exposure to heated PTFE dust or shavings through sources like a lit cigarette can be fatal.
-
What are the machining characteristics of PTFE Sheet?Machining PTFE Sheet can be challenging due to its softness, low friction, and "slipperiness." Proper care is required when holding the material in a lathe to prevent crushing or distortion. Additionally, long strings of swarf generated during machining can wrap around cutters or tooling.
-
What is the typical use of PTFE Sheet?PTFE Sheet is often used in applications requiring sliding action of parts, such as plain bearings and slide plates. It performs significantly better than nylon and acetal in low-friction applications. PTFE is also suitable for microwave frequencies in printed circuit boards due to its excellent dielectric properties. Additionally, PTFE sheets find application in cryogenic environments, and their high corrosion resistance makes them useful in laboratory settings as containers for materials like fluoroantimonic acid.
-
Is PTFE Sheet chemical resistant?PTFE exhibits excellent chemical resistance against most known elements and compounds. It is attacked only by alkaline metals in their elemental state, chlorine trifluoride, and elemental fluorine at high temperatures and pressures. PTFE does not dissolve in most solvents at temperatures up to around 300°C.
-
How does PTFE Sheet perform?PTFE products showcase exceptional resistance to high and low temperatures, chemical reaction, corrosion, and stress-cracking. Its electrical and low-friction properties make it a preferred material for various applications and processing techniques.
-
What are the unique characteristics of PTFE Sheet?PTFE's exceptional slipperiness is renowned, making it the only known surface to which a gecko cannot stick.
-
Is PEEK Sheet known as anything else?PEEK is also known by other trade names, including Victrex® PEEK, Arlon®, and Ketron®.
-
Does PEEK Sheet have Chemical resistance?PEEK Sheet material demonstrates resistance to a wide range of chemicals and solvents.
-
What are the unique characteristics of PEEK Sheet?PEEK Sheet exhibits exceptional radiation resistance, absorbing over 1000 units of radiation with no significant loss of mechanical properties.
-
What are the benefits of PEEK Sheet?PEEK polymer is renowned as one of the highest performing materials globally, offering a unique combination of properties. PEEK Sheet excels in high-temperature performance, displays excellent chemical and wear resistance, and is biocompatible. With a tensile strength of 90 to 100 MPa, PEEK Sheet can withstand demanding conditions. It boasts a high melting point of around 343°C, surpassing PTFE or PPS, and can operate at a continuous service temperature of 260°C. Moreover, PEEK Sheet is highly resistant to thermal degradation and immune to attacks by both organic and aqueous environments.
-
Can I glue PEEK Sheet?PEEK Sheet is challenging to bond due to its low surface energy. Depending on the adhesive used, surface roughening may improve bond strength.
-
What is the size range and availability of PEEK Sheet?PEEK Sheet material is available in natural (off-white) colour and comes in sheet thicknesses ranging from 5 mm up to 80mm.
-
What PEEK Sheet isn't suitable for?PEEK Sheet's stiffness decreases significantly, and its expansion rate increases above 150°C. For applications requiring close tolerance bearings or seals operating at temperatures higher than 150°C, an alternative material like PAI (polyamide-imide) may be a better choice.
-
Does PEEK Sheet have good wear resistance?PEEK Sheet exhibits very good abrasion and high wear resistance.
-
How does this amazing engineering plastic perform?PEEK Sheet boasts remarkable hardness, being 53% harder than Acetal, and possesses 36% more tensile strength than nylon 6,6, making it almost 60% stiffer. It excels in high-temperature applications, with a short-term operating temperature of 300°C, surpassing PTFE by 40 degrees. PEEK Sheet is known for its excellent machine-ability, flame retardancy, and exceptional wear and slide properties.
-
Why should you choose PEEK Sheet?PEEK polymer is celebrated as one of the highest performing materials globally. Its versatility makes it suitable for fabricating items used in demanding applications across various industries.
-
Can PEEK Sheet be machined easily?PEEK Sheet must undergo stress-relief through an annealing process before machining to prevent surface cracks and internal stresses. Silicon carbide cutting tools are recommended for natural PEEK Sheet, and machining dry is best to preserve its biocompatibility. If needed, pure water coolant may be used to remove cutting heat that builds up, as PEEK doesn't dissipate heat like metals.
-
Is PEEK Sheet suitable for food applications?All unfilled PEEK grades comply with FDA regulations for repeated food contact.
-
What are the drawbacks of PEEK Sheet?The main disadvantage lies in the relatively high price of PEEK, nearly four times that of PTFE, which often restricts its use to high-value items. Another drawback is that PEEK is not a shape memory polymer, meaning it lacks the ability to return to its original shape after temporary deformation through an external stimulus.
-
What grade of PEEK Sheet do you supply?We supply the 450g grade of PEEK Sheet..
-
What is PEEK Sheet used for?PEEK Sheet's exceptional strength makes it ideal for fabricating items used in demanding applications, such as bearings, piston parts, pumps, HPLC columns, compressor plate valves, and cable insulation. It is extensively utilised in aerospace, automotive, and chemical process industries, as well as train and underground applications. Moreover, PEEK serves as a metal replacement for high-temperature uses and has become crucial in the oil and gas industry for drilling and production. Additionally, PEEK plays a superior role in alternative energy production, contributing to the construction of solar, wind, nuclear, geothermal, and hydropower equipment and components.
-
Is there a summary of PEEK Sheet?PEEK is a unique, high-temperature, high-performance engineering plastic. Its exceptional properties make it tough, rigid, and remarkably strong, with excellent chemical and radiation resistance. PEEK's applications are extensive, from steam and high-pressure water environments to vacuum conditions, where it shows no significant degradation. The material's smoke and toxic acid gas release during combustion are the lowest of any thermoplastic. PEEK's insolubility in common solvents and resistance to a wide range of organic and inorganic liquids, even at high temperatures, further add to its versatility.
-
When would you not choose PEEK Sheet?While PEEK Sheet excels in high-end applications, its cost can be prohibitive for most low-end or low-cost components.
-
Is there a summary of RG1000 Sheet?RG1000 Sheet, also known as "regen," is a versatile and cost-effective alternative to virgin UHMWPE. It offers excellent sliding and abrasion performance, making it suitable for a wide range of applications. However, it is essential to note that RG1000 Sheet is not FDA approved and should not be used in food contact applications.
-
Is RG100 chemical resistant?RG1000 is highly resistant to corrosive chemicals, except for oxidising acids.
-
What is the size range and availability of RG1000 Sheet?RG1000 Sheet is commercially available in two common sizes of 2000mm X 1000mm and 3000mm X 1250mm, with thicknesses ranging from 5 mm to 80mm. It is currently only available in black or green.
-
What to be aware of when using RG1000 Sheet?RG1000 Sheet is a regenerated grade that offers almost identical performance to virgin grade RG1000 Sheet at a reduced price, making it suitable for projects on a budget or those that do not require FDA approval.
-
Is it possible to glue RG1000?All UHMWPE plastics, including RG1000, do not absorb water readily, nor wet easily, making bonding difficult.
-
How does RG1000 Sheet perform?RG1000 Sheet, also known as "regen," is the recycled grade of UHMWPE. It offers sliding and abrasion performance close to that of virgin grade. This material is suitable for low friction sliding applications and is commonly used in areas that do not require the unique properties of virgin UHMWPE, such as Food or Pharmaceutical. RG1000 Sheet has an incredibly low coefficient of friction, providing components with a high lifespan and minimal drag. It is resistant to many dilute acids, solvents, and cleaning agents.
-
Where should RG1000 Sheet not be used?RG1000 Sheet is not suitable for food contact applications or medical uses.
-
What are the unique characteristics of RG1000?RG1000 has a significantly lower coefficient of friction than nylon and acetal, comparable to that of PTFE or Teflon, while offering better abrasion resistance than PTFE. It has a slippery surface texture that feels almost waxy.
-
Is RG1000 wear resistant?Yes, RG1000 sheet is highly resistant to abrasion, even more so than carbon steel in some forms.
-
Is RG1000 suitable for food applications?RG1000 is not approved for any use in food applications.
-
Why is RG1000 Sheet the right choice?RG1000 Sheet is very similar to Virgin UHMWPE but comes with a definite price advantage. It exhibits an exceptionally low coefficient of friction, providing superb sliding properties and exceptional wear and abrasion resistance. The sheet is tough even at low temperatures, lightweight, and easy to weld, although bonding can be challenging.
-
What is RG1000 Sheet used for?Due to its excellent abrasion resistance, RG1000 Sheet is often used for lining chutes, hoppers, slide-ways, and wear blocks in aggressive environments. It is also suitable for marine applications with high demand, thanks to its low moisture absorption. However, it should only be used for non-FDA applications, such as forest-product drag conveyor flights, conveyor-chain wear plates, and belt-conveyor wipers and skirts.
-
What are the advantages of RG1000 Sheet?RG1000 has no odour and is non toxic while it is also tasteless. Furthermore, it is economical and offers a low level of moisture absorption. It is self lubricating and has a low level of friction while it is resistant to water and a wide range of chemicals.
-
What are the drawbacks of RG1000 Sheet?RG1000 Sheet has some limitations, including a maximum operating temperature of 90°C, a short-term operating temperature of 120°C, and a melting point of around 135°C. It may not be well-suited for high tensile applications. Since it is a recycled version of UHMWPE, it may not be compatible in all aspects. Additionally, it is not FDA approved, as there is no white/natural grade available.
-
What are the machining characteristics of RG1000 Sheet?When machining RG1000 Sheet, it is recommended to use high-speed steel tooling with ample back rake, side rake, clearances, and a generous nose radius. Clamping parts without distortion can be challenging, and when drilling, the drill may tend to screw into the material.
-
Can PVC Sheet be used in food applications?PVC sheet is not currently FDA approved for direct and permanent contact with food.
-
Does PVC Sheet have any wear resistance?PVC sheet exhibits mediocre resistance to wear and abrasion compared to Nylon and UHMWPE. It is tough but can become more brittle at temperatures below zero.
-
Is PVC Sheet easy to bond with adhesives?Glueing PVC is relatively easy, and various adhesives like solvent cements, contact adhesives, and super glue work well. High-frequency welding (glueing) is also possible.
-
Is PVC Rod known as anything else?Other Trade names (also known as): Boltaron® Geon® Vintec® Corzan®
-
What are the benefits of PVC Sheet?PVC sheet offers several advantages, including good hardness and mechanical properties, excellent electrical insulating properties, and very high chemical and moisture resistance. It also exhibits excellent forming characteristics, good dimensional stability, and is easily bondable, making it an excellent choice for welding. Moreover, PVC is self-extinguishing and relatively inexpensive.
-
How does PVC Sheet perform?PVC sheet material has good hardness and is known for its high temperature resistance, with a short-term operating temperature of 300°C, which is 15% higher than PTFE. It is 53% harder than Acetal and has 36% more tensile strength than nylon 6, 6. PVC also possesses excellent machine-ability, wear resistance, and slide properties. Additionally, it is flame retardant.
-
Does PVC Sheet have Chemical resistance?PVC sheet is generally suitable to withstand a wide range of chemicals, but it may not be compatible with certain solvents that cause swelling and softening of the material.
-
Why would you choose not to use PVC Sheet?While PVC sheet has various applications, it may not be the ideal choice for components that require very high wear resistance, continuous contact with food products, or items needing significant flexibility, low friction, or high-temperature resistance.
-
What is PVC Sheet used for?PVC sheet finds applications in chemical processing tanks, valves, fittings, and piping systems. It is also used for cladding, electrical insulators, acid tanks, templates, fabricated fittings, and battery boxes.
-
What is the size range and availability of PVC Sheet?Our PVC sheets are available in grey colour and come in thicknesses ranging from 1.5mm up to 50mm.
-
Why should you choose PVC Sheet?PVC sheet is an extremely durable material that is much stronger than some other plastics. It can typically withstand impacts many times that which completely shatter components made of Acrylic or Styrene, for example. PVC is extremely chemical resistant and resists attack or degradation from a wide range of chemicals, making it the material of choice in many tough industrial applications.
-
What are the drawbacks of PVC Sheet?PVC's heat stability is limited, as it starts to decompose at 140°C and melts at 160°C. While it is a good insulator, its electrical insulating property is not as high as that of plastics such as polyethylene and polypropylene, making it more suitable for medium or low voltage and low-frequency insulation materials.
-
What are the machining characteristics of PVC Sheet?PVC is quite hard and machines well, providing a nice machined finish. Double-edged milling cutters are recommended, and circular saws with hard metal-inserted teeth and a tooth spacing of 10 to 20 mm are effective for sawing.
-
What are the unique characteristics of PVC Sheet?PVC pipes have been analysed after over 35 years of in-ground use, showing no detectable corrosion or degradation and an estimated additional 50 years of service life.
-
Is there a summary of PVC Sheet?PVC sheet is a durable, tough material that is resistant to chemicals, acids, weather, and abrasion. It can be machined and tooled into a vast variety of shapes and components. It is strong yet relatively lightweight, affordable, and widely available. While it has a low melting point in comparison to other plastics, this is a great advantage to fabricators. PVC sheet is known for its self-extinguishing properties, making it a safe choice in various applications.
-
Can Whale Tufnol Sheet be glued and bonded?Whale Tufnol can be bonded to various materials using appropriate adhesives.
-
Is Whale Tufnol Sheet suitable for food applications?Whale Tufnol Sheet should not be used in any food applications that involve direct contact with food products.
-
Is 1P/13 Tufnol Sheet chemical resistant?1P/13 Tufnol Sheet does not have high resistance to chemicals or acids.
-
What is the size range and availability of 10G/40 Tufnol Sheet?We stock thicknesses of 10G/40 Tufnol Sheet from 1.6mm up to 16mm, and other sizes may be available to order.
-
What should Kite Tufnol Sheet not be used for?Kite grade Tufnol Sheet is not recommended for general purpose applications as it is not as strong as 1P/13 grade or Whale grade. It is also not suited for high wear applications.
-
What is Tufnol Whale Sheet?Tufnol Whale Sheet is a grade of engineering plastic specifically designed for mechanical engineering purposes. It is made of medium weave cotton and phenolic resin laminated plastic material. This grade offers excellent dimensional stability and can be used either dry or lubricated with water, oils, or grease. It possesses desirable physical properties, including high strength, good toughness, and wear resistance. Tufnol Whale Sheet is suitable for applications requiring wear-resistant components such as bearings, bushes, spacers, and low voltage applications.
-
Is there a summary of Kite Tufnol Sheet?Kite Tufnol sheet is a first-class electrical insulating material with good dielectric strength and high insulation resistance. It has low moisture absorption and good mechanical strength, but its impact strength is lower than that of most other grades of Tufnol. It machines easily and can be hot punched in thicknesses up to 3.2mm. It is used for a multitude of applications at low, medium, and high voltages, such as terminal boards, mounting panels, tag strips, coil formers, insulating sleeves and bushes, busbar supports, tool and instrument handles, coil supports, insulated enclosures, brush holders, insulating spacers, and special purpose plugs and sockets. —----------------------------------------- Tufnol 10G/40 Sheet SRBGF - Synthetic Resin Bonded Glass Fabric Mechanical Properties Density: 1.90/cm3 Cross breaking strength: 490 MPa Charpy impact strength (notched): 60 kJ/m2 Tensile strength: 355 MPa Young's modulus: 17.7 GPa Thermal Properties Maximum working temperature – continuous: 130°C Maximum working temperature – intermittent: 150°C Thermal classification: B
-
Why not choose Whale Tufnol Sheet?A downside to the production process of Whale Tufnol Sheet is that tolerances can vary due to factors like the number and thickness of individual sheets used, pressure applied by the press, or variations in steel press sheets. It may not be suitable for applications requiring minimal tolerances.
-
What are the advantages of 10G/40 Tufnol Sheet?10G/40 Tufnol Sheet offers the following advantages: High strength Rigidity Dimensional stability
-
How well does Whale Tufnol Sheet perform?Whale Tufnol Sheet is produced similarly to plywood, making it quite rigid, up to twice as much as nylon. This inherent rigidity reduces creep, providing stability under stress. In comparison to nylon, Whale Tufnol Sheet exhibits less creep under torque, resulting in better bolt retention.
-
What should 10G/40 Tufnol Sheet not be used for?Due to the abrasive nature of the high glass fibre content, 10G/40 Tufnol Sheet is not suitable for bearing or wearing applications.
-
Is Kite Tufnol Sheet suitable for food applications?Kite Tufnol Sheet is not suitable for constant contact with food.
-
Is Whale Tufnol Sheet good for wear resistance?Yes, Whale Tufnol Sheet is known for its very good wear resistance and toughness.
-
What is the size range and availability of Kite Tufnol Sheet?We stock thicknesses of Kite Tufnol Sheet from 1mm up to 25mm.
-
What is the size range and availability of Whale Tufnol Sheet?Whale Tufnol Sheet is available in brown or tan colour and in thickness ranging from 1 mm up to 50mm. Thicker materials may be obtained through our sales team.
-
What should Whale Tufnol Sheet not be used for?Whale Tufnol Sheet is not suitable for high electrical insulation applications, circuit boards, or covers.
-
What are the disadvantages of 1P/13 Tufnol Sheet?1P/13 Tufnol Sheet has the following disadvantages: Prone to chipping under high impact Not suitable for high voltage applications Low flame retardancy
-
What are the disadvantages of 10G/40 Tufnol Sheet?10G/40 Tufnol Sheet has the following disadvantages: SRBGF is very abrasive Not suitable for cost-critical lower voltage applications
-
Is 1P/13 Tufnol Sheet good for wear resistance?1P/13 Tufnol Sheet is more suited for general-purpose use and router jigs, but for high wear resistance, the Whale grade is recommended.
-
Is 1P/13 Tufnol Sheet suitable for food applications?1P/13 Tufnol Sheet is not suitable for constant contact with food.
-
Is there a summary of 1P/13 Tufnol Sheet?1P/13 Grade Tufnol Sheet, an economical commercial paper-based laminate, presents moderate electrical properties. Outshining other phenolic paper grades, it boasts higher mechanical strength and superior impact resistance. Ideal for low voltage insulation applications, this grade allows easy machining for versatile components. Its affordability makes it a practical choice for less demanding mechanical tasks such as spacers, base plates, side plates, and simple jigs and fixtures. Tufnol Sheet 1P/13 delivers reliable performance while remaining cost-effective for various industrial applications. —----------------------------------------- Tufnol Kite Sheet SRBP - Synthetic Resin Bonded Paper Mechanical Properties Density: 1.36/cm³ Cross breaking strength: 175 MPa Charpy impact strength (notched): 2.7 kJ/m2 Shear strength (flatwise): 350 MPa Compressive strength (edgewise): 200 MPa Thermal Properties Maximum working temperature – continuous: 90°C Maximum working temperature – intermittent: 120°C Thermal classification: E
-
Is Whale Tufnol Sheet chemical resistant?Whale Tufnol Sheet has good resistance to chemicals, oils, solvents, and hydrocarbons, although concentrated acids and alkalis may attack the laminates.
-
What should 1P/13 Tufnol Sheet not be used for?1P/13 Tufnol Sheet is not recommended for high wear applications or for high voltage electrical applications.
-
Are there any unique characteristics for Whale Tufnol Sheet?Whale Tufnol Sheet is made primarily of cotton sheets and phenolic chemical resin, pre-soaked and cured to create a tightly bonded sheet. Its production process involves high pressure and heat, resulting in a rigid and stable material.
-
Is there a summary of 10G/40 (SRBGF) Sheet?Tufnol Grade 10G/40, also referred to as SRBGF, offers exceptional performance in diverse applications that demand high strength, rigidity, dimensional stability, and electrical properties. It finds common use in insulation for large turbine generators, components of cryogenic superconducting magnets, and structural insulation for high-performance electronic equipment, among others. However, due to the abrasive nature of its high glass fibre content, it is not recommended for wearing or bearing applications. Tufnol Grade 10G/40 remains a top choice for critical roles requiring reliability and resilience.
-
What is 10G/40 Tufnol Sheet used for?10G/40 Tufnol Sheet is used for insulation in high-performance electrical applications, structural insulation, and jigs.
-
What are the disadvantages of Kite Tufnol Sheet?Kite Tufnol Sheet has the following disadvantages: Prone to chipping under high impact Low flame retardancy
-
Is 10G/40 Tufnol Sheet suitable for food applications?No, 10G/40 Tufnol Sheet is not suitable for contact with food.
-
What is Kite grade Tufnol Sheet used for?Kite grade Tufnol Sheet is more suited to higher voltage electrical insulation applications.
-
How well does Whale Tufnol Sheet machine?Whale Tufnol Sheet cannot be melted to reshape it. Finished components are made by machining using conventional machine tools such as saws, drills, lathes, milling machines, or CNC machines. It is easily machined to produce finished components, but delicate parts may be subject to shearing along the lamination.
-
What are the disadvantages of Whale Tufnol Sheet?Whale Tufnol Sheet is suitable for electrical insulation but only at low voltages. Its maximum working temperature is limited to 120 to 130 degrees Celsius, and when machined, it produces a fine yellow dust.
-
Why should you choose Whale Tufnol Sheet?Whale Tufnol Sheet is an excellent thermal barrier material, providing protection against extreme heat and cold transfer. It is hard, rigid, strong, and lightweight, making it a good electrical insulator and resistant to long-term immersion in water. It exhibits exceptional weather resistance and has been used for outdoor and marine components for many decades without corroding or degrading.
-
What is 1P/13 Tufnol Sheet used for?1P/13 Tufnol Sheet is described as the "general purpose" grade and is commonly used for router jigs, fixtures, guides, and basic tooling.
-
Is Kite Tufnol Sheet chemical resistant?Kite Tufnol Sheet does not have very high resistance to chemicals or acids.
-
Is there a summary of Whale Tufnol Sheet?Whale Tufnol Sheet, a Synthetic Resin Bonded Fabric (SRBF), is crafted from medium weave cotton and phenolic resin laminated plastic. As a go-to choice for mechanical applications, it offers exceptional all-around strength, good toughness, wear resistance, and thermal barrier properties. Its versatility and ease of handling make it a preferred option, while its outstanding rigidity ensures reliable performance. Whale Tufnol Sheet stands as a reliable, general-purpose medium weave grade, catering to a wide range of mechanical requirements with unmatched strength and resilience. —----------------------------------------- Tufnol 1P/13 Sheet SRBP - Synthetic Resin Bonded Paper Mechanical Properties Density: 1.36/cm³ Tensile strength: 164 MPa Cross breaking strength: 175 MPa Charpy impact strength (notched): 3.9 kJ/m2 Shear strength (flatwise): 100 MPa Thermal Properties Maximum working temperature – continuous: 90°C Maximum working temperature – intermittent: 120°C Thermal classification: E
-
How well does Kite Tufnol Sheet machine?Kite grade Tufnol Sheet machines quite well with carbide cutters, but it generates a fine yellow dust during the machining process.
-
Can 10G/40 Tufnol Sheet be glued and bonded?Yes, 10G/40 Tufnol Sheet can be easily bonded with many commercially available adhesives.
-
Can Kite Tufnol Sheet be glued and bonded?Kite Tufnol Sheet can be easily bonded with many commercially available adhesives such as araldite, epoxies, and contact adhesives.
-
Can 1P/13 Tufnol Sheet be glued and bonded?1P/13 Tufnol Sheet can be easily bonded with commercially available adhesives such as araldite, epoxies, and contact adhesives.
-
What is Whale Tufnol Sheet used for?Whale Tufnol Sheet is a versatile material used in a wide range of mechanical applications and general uses. It is commonly used for gears, spacers, jigs and fixtures, wear-resistant components, and low voltage insulation applications.
-
How well does 10G/40 Tufnol machine?10G/40 Tufnol machines well, but due to its abrasive nature, it can be hard on tooling.
-
What are the advantages of Kite Tufnol Sheet?Kite Tufnol Sheet offers the following advantages: Suitable for high voltage applications Lightweight Rigid and strong Economical
-
What are the advantages of Whale Tufnol Sheet?Whale Tufnol Sheet offers several advantages, including rigidity with high strength and low weight, good electrical and thermal insulation properties, and resistance to corrosion in metal parts. It exhibits excellent weather resistance and has good resistance to chemicals, oils, solvents, and hydrocarbons.
-
How well does 1P/13 Tufnol Sheet machine?1P/13 grade can be machined well with carbide cutters, but it generates a fine yellow dust during the machining process.
-
What are the advantages of 1P/13 Tufnol Sheet?1P/13 Tufnol Sheet offers the following advantages: Very strong and rigid plastic Lightweight Economical Reasonable low voltage insulation
-
What is the size range and availability of 1P/13 Tufnol Sheet?We stock thicknesses of 1P/13 Tufnol Sheet from 1mm up to 25mm.
-
Is Kite Tufnol Sheet good for wear resistance?Kite Tufnol Sheet is more suitable for general-purpose use and can withstand being used as a router jig, but the Whale grade is more designed for wear resistance.
-
How does UHMWPE Sheet perform?UHMWPE Sheet exhibits exceptional resistance to abrasion and is one of the best materials for lining chutes and hoppers in highly abrasive environments, such as quarries. It has an incredibly low coefficient of friction, making it ideal for guiding containers along conveyors in food production environments. Its resistance to moisture absorption also makes it suitable for marine applications and some cryogenic components. Additionally, UHMWPE is increasingly used in various industrial applications, including automotive, manufacturing, and bottling sectors.
-
What is unique about UHMWPE Sheet?UHMWPE Sheet can also be obtained in a regenerated grade known as RG1000, which offers similar performance to virgin grade UHMWPE Sheet at a reduced price, making it a budget-friendly option for certain projects.
-
Is there a summary of UHMWPE Sheet?UHMWPE Sheet is a high-performance engineering plastic with exceptional abrasion resistance and a low coefficient of friction. It is tough, lightweight, and maintains its properties even in cryogenic conditions. This versatile material finds applications in various industries, including quarrying, food production, marine environments, and industrial sectors like automotive and bottling.
-
What are the machining characteristics of UHMWPE Sheet?High-speed steel tooling with proper rake and clearances is recommended for machining UHMWPE Sheet. However, clamping UHMWPE parts without distortion can be challenging, and drills may tend to screw into the sheet material when drilling.
-
What is the wear resistance of UHMWPE Sheet like?UHMWPE Sheet is highly resistant to abrasion, making it 15 times more resistant than carbon steel in some forms.
-
Is UHMWPE Sheet safe for food applications?Natural grade UHMWPE is FDA approved for use in food applications.
-
Why should you choose UHMWPE Sheet?UHMWPE Sheet offers a unique combination of outstanding properties, including superior abrasion resistance, impact resistance, and self-lubrication. It is a versatile engineering plastic that can be machined into various parts at a competitive price.
-
What are the advantages of UHMWPE Sheet?UHMWPE Sheet offers several advantages: Odourless, tasteless, and nontoxic Extremely low moisture absorption Very low coefficient of friction Maintains toughness even at temperatures below −150°C Self-lubricating and highly abrasion resistant Resistant to water, moisture, and most chemicals Resistant to microorganisms
-
What is the size range and availability of UHMWPE Sheet?UHMWPE Sheet is available in two common sizes: 2000mm X 1000mm and 3000mm X 1250mm. It comes in thicknesses ranging from 2mm to 250mm and is available in natural (white), black, and green colours.
-
What are the disadvantages of UHMWPE Sheet?UHMWPE Sheet has the following disadvantages: Melting point around +130°C to +136°C Not advisable to use UHMWPE at temperatures exceeding 80°C to 100°C for extended periods Under load, UHMWPE will deform continually as long as the stress is present, an effect known as creep May not be suitable for high load applications
-
Can UHMWPE Sheet be glued or bonded?UHMWPE does not absorb water readily, making it difficult for adhesives to bond effectively, resulting in low shear strength.
-
What is UHMWPE Sheet used for?UHMWPE Sheet is commonly used for lining chutes and hoppers in harsh and abrasive environments, as well as for guiding containers along conveyors in food production settings. Its low moisture absorption makes it suitable for marine applications and some cryogenic components. It is also utilised in various industrial applications, including automotive, manufacturing, and bottling sectors.
-
Is UHMWPE Sheet chemical resistant?Yes, it is extremely resistant to corrosive chemicals although not oxidising acids.
-
Does UHMWPE Rod have good wear resistance?UHMWPE Rod is highly resistant to abrasion, being 15 times more resistant than carbon steel in some forms.
-
Why should you choose UHMWPE Rod?UHMWPE Rod offers exceptional abrasion resistance, superior impact resistance, non-sticking and self-lubricating properties, and excellent mechanical properties even in cryogenic conditions. It is a versatile material that can be machined into various shapes and parts at a competitive price.
-
Is UHMWPE Rod suitable for food applications?Natural grade UHMWPE is FDA approved for use in food applications.
-
What is UHMWPE Rod used for?UHMWPE Rod is commonly used for wear-resistant applications such as sand, gravel, or aggregate process applications, as it can withstand harsh conditions. It is also used in low friction pulleys and for guiding containers along conveyors in food production environments. Its low moisture absorption makes it suitable for marine applications, and it is also utilised in cryogenic components due to its low temperature capabilities. Moreover, UHMWPE Rod finds industrial applications in sectors like automotive and bottling. It is a popular material for orthopaedic and spine implants in total joint arthroplasty since the 1960s.
-
Is there a summary of UHMWPE Rod?UHMWPE Rod is a high-performance engineering plastic with remarkable resistance to abrasion, low friction, and excellent mechanical properties. It finds extensive applications in various industries due to its unique combination of characteristics, including toughness, self-lubrication, and resistance to water, chemicals, and extreme temperatures.
-
What are the advantages of UHMWPE Rod?UHMWPE Rod offers the following advantages: Odourless, tasteless, and nontoxic Extremely low moisture absorption Very low coefficient of friction Self-lubricating and highly resistant to abrasion Very resistant to water, moisture, and most chemicals Resistant to microorganisms Retains toughness even at temperatures below −150°C
-
What are the disadvantages of UHMWPE Rod?UHMWPE Rod has the following disadvantages: Melting point around 130°C to 136°C Not suitable for prolonged use at temperatures exceeding 80°C to 100°C Susceptible to deformation under continuous stress (creep) May not be suitable for high load applications
-
Is UHMWPE Rod chemical resistant?It exhibits high resistance to corrosive chemicals except oxidising acids.
-
Can UHMWPE Rod be glued?UHMWPE does not absorb water readily, nor does it wet easily, which makes bonding it to other polymers difficult.
-
What are the machining characteristics of UHMWPE Rod?High-speed steel tooling with back rake, side rake, and clearances, along with a generous nose radius, is recommended for machining UHMWPE Rod. Caution should be exercised when turning it as the chips can be continuous and tend to wrap around the tooling.
-
What is the size range and availability of UHMWPE Rod?We stock UHMWPE Rod in diameters ranging from 20mm up to 200mm, available in natural opaque colour (often described as white) or black.
-
Does UHMWPE Rod have any unique characteristics?UHMWPE Rod has a significantly lower coefficient of friction compared to nylon and acetal, making its surface feel slippery and almost waxy.
-
How does UHMWPE Rod perform?UHMWPE Rod has exceptional resistance to abrasion and outperforms almost any engineering plastic. It exhibits very low friction and provides a long-lasting bearing medium. It is also resistant to many dilute acids, solvents, and cleaning agents. With a maximum operating temperature of around 90°C and a short-term operating temperature of 120°C, UHMWPE Rod is a tough material with the highest impact strength among thermoplastics.
-
What is Tufnol Rod used for?Tufnol Rod is a versatile material used in a wide range of mechanical applications and general uses. Common applications include spacers, rollers, jigs and fixtures, wear-resistant components, low voltage insulation, and more.
-
What are the disadvantages of Tufnol Rod?Tufnol Rod has a few drawbacks, including its unsuitability for use as washers or gears. It is suitable only for low voltage applications and may produce dust during machining. Additionally, it can be challenging to produce very intricate or delicate parts with Tufnol Rod.
-
Why should you choose Tufnol Rod?Tufnol Rod is a non-metallic material with excellent properties. It is hard, rigid, strong, and lightweight, making it suitable for various mechanical applications. It also offers good electrical insulation and weather resistance, as well as resistance to wear and abrasion.
-
Does Tufnol Rod have good wear resistance?Yes, Tufnol Rod has good wear resistance and toughness.
-
Can Tufnol Rod be glued and bonded?Tufnol can be bonded to various materials using appropriate adhesives, such as araldite, epoxy, and contact adhesives.
-
Why not choose Tufnol Rod?Tufnol Rod is not suitable for gears or washers due to its layered construction. It is not recommended for high electrical insulation applications.
-
Is Tufnol Rod chemical resistant?Tufnol has good resistance to chemicals, oils, solvents, and hydrocarbons, although concentrated acids and alkalis may attack laminates.
-
What should Tufnol Rod not be used for?Tufnol Rod is not suitable for circuit board parts, covers, and high electrical insulation applications.
-
How well does Tufnol Rod perform?Tufnol Rod, similar to plywood, is quite rigid, up to twice as much as nylon. Its inherent rigidity reduces creep, making it more stable under stress. In comparison to nylon, Tufnol Rod exhibits less creep when subjected to torque, resulting in better bolt retention. Tufnol Rod performs well in low friction sliding applications and offers excellent wear resistance and toughness.
-
How well does Tufnol Rod machine?Tufnol Rod cannot be melted to re-shape it, so finished components are made by machining using conventional machine tools like saws, drills, lathes, milling machines, or CNC machines. Machining Tufnol can produce dust and may cause the material to melt and adhere to the cutting tool. Delicate machined components are subject to shearing due to its plywood-like construction.
-
Is Tufnol Rod suitable for food applications?Tufnol should not be used in any food applications where it may come into contact with food products.
-
What are the advantages of Tufnol Rod?Tufnol Rod offers several advantages, such as rigidity with high strength and low weight, good electrical and thermal insulation properties, and a maximum working temperature of around 120 to 130 degrees Celsius, which is higher than nylon. It is non-corrosive and can reduce corrosion in metal parts. Tufnol Rod is resistant to heavy loads with minimal creep and exhibits excellent weather resistance, as well as good resistance to chemicals, oils, solvents, and hydrocarbons.
-
What is the composition of Tufnol Rod?Tufnol Rod, specifically Whale Tufnol Rod, is a medium weave cotton and phenolic resin laminated plastic material designed for mechanical engineering purposes. It is suitable for wear-resistant components such as bearings, bushes, spacers, and low voltage applications. Tufnol Rod is dimensionally stable and can be used either dry or lubricated with water, oils, or grease. It offers excellent physical properties, including rigidity, strength, toughness, and wear resistance.
-
Are there any unique characteristics for Tufnol Rod?Whale Tufnol is made primarily of cotton sheets and phenolic chemical resin, pre-soaked, and cured to create a tightly bonded rod. The production process involves crushing and curing under high pressure and heat. Finished rods have a smaller diameter than their original size. Tufnol Rod has inherent rigidity and stability, similar to plywood.
-
What is the size range and availability of Tufnol Rod?Tufnol Whale Rod is available in brown (light tan colour) and in diameters ranging from 6mm up to 100mm. Larger diameters are also available.
-
Is there a summary of Tufnol Rod?Tufnol Rod, also known as Whale Tufnol, is a versatile and durable material designed for mechanical engineering applications. It offers rigidity, strength, and toughness, making it suitable for various components in wear-resistant and low voltage applications. While it is not suitable for high electrical insulation or delicate parts, Tufnol Rod performs well in sliding applications and exhibits excellent wear resistance and dimensional stability.
-
What are the unique characteristics of PVC Rod?PVC pipes have shown exceptional resistance to corrosion and degradation even after in-ground use for over 35 years, with an estimated additional 50 years of service life.
-
What is PVC Rod used for?PVC rod finds applications in chemical processing tanks, valves, fittings, and piping systems. It is also utilised in pump components, electrical insulators, acid tanks, templates, fabricated fittings, and battery boxes.
-
Is PVC Rod okay for food applications?PVC rod is not FDA approved, so direct and permanent contact with food is not recommended.
-
Does PVC Rod have good wear resistance?PVC rod exhibits reasonable resistance to high wear and abrasion.
-
What are the benefits of PVC Rod?PVC rod offers numerous advantages, including good hardness and mechanical properties, excellent electrical insulating properties, very high chemical resistance, and good moisture resistance. It also exhibits good dimensional stability, is easily bondable, and serves as an excellent engineering plastic for welding. Moreover, PVC is self-extinguishing and relatively inexpensive.
-
Why you wouldn't use PVC Rod?While PVC rod has various applications, it may not be the ideal choice for high wear applications like nylon or UHMWPE. Additionally, it is not recommended for components in constant contact with food products or those requiring great flexibility, low friction, or high temperature resistance.
-
What is the size range and availability of PVC Rod?PVC rods are available in grey colour from stock, with black, red, and cream colours available within a day or two of order. The diameters range from 6mm up to 300mm.
-
Is PVC Rod known as anything else?PVC rod is known by other trade names, including Boltaron®, Geon®, Vintec®, and Corzan®.
-
Is PVC Rod chemical resistant?In general, PVC is suitable to withstand most strong acids, alkalis, aqueous solutions, and more, but it should not be used with certain solvents that lead to swelling and softening of the material.
-
Is there a summary of PVC Rod?PVC rod is a durable and chemical-resistant material that can be machined and tooled into various shapes and components. It offers good electrical insulation properties and finds applications in industrial settings due to its strength and longevity. PVC is an excellent choice for engineering applications and provides reliable performance over time.
-
What are the machining characteristics of PVC Rod?PVC is reasonably hard, and when sawing, it is best to use circular saws with hard metal-inserted teeth and a tooth spacing of 10 to 20 mm. Double-edged milling cutters are recommended for machining PVC.
-
How does PVC Rod perform?PVC products are known for their longevity, with lifespans of up to and over 60 years. This reliability leads to reduced maintenance and repair needs. PVC is widely used in building and construction applications due to its resistance to oxidation and degradation and excellent fire resistance from its inherent chlorine content.
-
Why is PVC Rod right for you?PVC rod is a durable material with strong mechanical properties, resistance to chemicals and weather, and good electrical insulation. Its affordability and wide availability make it suitable for various applications.
-
Is it easy to glue and bond PVC Rod?Glueing or bonding PVC is straightforward, but it is generally a permanent process, making undoing the bond challenging. High-frequency welding (glueing) is possible.
-
What are the drawbacks of PVC Rod?PVC's heat stability is limited, as it starts to decompose at 140°C and melts at 160°C. While it is a good insulator, its electrical insulating property is not as high as that of polyethylene or polypropylene, making it more suitable for medium or low voltage and low frequency insulation materials.
-
Can PEEK Rod be glued or bonded?PEEK Rod's low surface energy makes it challenging to glue, and bonding may require specialised adhesives. Surface roughening may have a positive effect on adhesion.
-
Does PEEK Rod have good wear resistance?PEEK exhibits very good abrasion and high wear resistance.
-
Is PEEK Rod suitable for food applications?Natural PEEK grades comply with FDA regulations for extensive food contact.
-
What is the size range and availability of PEEK Rod?PEEK Rod is available in natural (off-white) colour and in diameters ranging from 5 mm up to 180mm.
-
Is PEEK Rod Chemical Resistant?PEEK Rod demonstrates resistance to a wide range of chemicals and solvents.
-
What is PEEK Rod not suitable for?PEEK Rod's stiffness drops off significantly, and its expansion rate increases above 150°C. In such cases, alternative materials like PAI (polyamide-imide) may be a better choice for close tolerance bearings or seals operating at temperatures above 150°C.
-
What are the drawbacks of PEEK Rod?The main disadvantage of PEEK Rod is its relatively high price, which can be up to four times that of PTFE. This cost factor often limits its application to high-value items. Additionally, PEEK is not a shape memory polymer and lacks the ability to return from a temporarily deformed state to its original shape by an external stimulus like a temperature change.
-
What is the typical use of PEEK Rod?PEEK Rod is widely used to fabricate items for demanding environments, such as bearings, piston parts, pumps, and compressor plate valves. It finds extensive application in aerospace, automotive, and chemical process industries. Moreover, PEEK is compatible with vacuum applications and serves as a metal replacement for high-temperature uses, making it a key material for various industries, including the oil and gas sector. It also plays a crucial role in alternative energy production for constructing equipment and components in solar, wind, nuclear, geothermal, and hydropower.
-
What are the benefits of PEEK Rod?PEEK Rod is considered one of the highest performing materials worldwide, offering a unique combination of properties. It boasts excellent high-temperature performance, with a high continuous service temperature of 260°C and a melting point of 343°C, higher than that of PTFE or PPS. PEEK Rod also exhibits a high tensile strength of 90-100 MPa, as well as exceptional chemical and wear resistance. It is biocompatible and highly resistant to attack by both organic and aqueous environments.
-
Is PEEK Rod known as anything else?PEEK is also known by other trade names, including Victrex® PEEK, Arlon®, and Ketron®.
-
Is there a summary of PEEK Rod?PEEK is a unique and high-performance engineering plastic, exhibiting exceptional thermal stability, chemical resistance, and radiation resistance. Its superior mechanical properties and low coefficient of friction make it an ideal choice for various applications, particularly in demanding environments.
-
How does PEEK Rod machine?PEEK Rod requires stress-relief through an annealing process before machining to prevent surface cracks and internal stresses. Silicon carbide cutting tools are recommended for natural PEEK Rod, and dry machining is best to preserve its biocompatibility. However, PEEK does not dissipate heat like metals, and in certain cases, a coolant such as pure water may be used to dispel the cutting heat.
-
Why should you choose PEEK Rod?PEEK Rod offers outstanding performance with its robustness and high-temperature capability. Its use in demanding applications and compatibility with vacuum applications make it an excellent choice for various industries.
-
How does PEEK Rod perform?PEEK Rod excels in high-temperature applications, with a short-term operating temperature of 300°C, 40 degrees higher than PTFE, making it 15% higher. It is 53% harder than Acetal and possesses 36% more tensile strength than nylon 6, 6, while being almost 60% stiffer. PEEK Rod exhibits excellent machine-ability, flame retardancy, and wear and slide properties.
-
What are the unique characteristics of PEEK Rod?PEEK's exceptional radiation resistance makes it unique, as it can absorb over 1000 units of radiation without a noticeable loss of mechanical properties.
-
Why not choose PEEK Rod?Despite its excellent properties, the high cost of PEEK Rod may make it unsuitable for most low-end or low-cost components.
-
Is PTFE Rod suitable for food applications?PTFE is commonly used in cookware linings, making it an approved food-grade material.
-
Is there a summary for PTFE Rod?PTFE, famously known as Teflon®, stands as a thermo-set plastic that retains its shape, flexibility, and resilience under stress, tension, or compression. Highly versatile, it can be moulded into various shapes, sizes, and hardness levels. PTFE showcases superior abrasion, ageing, and tear resistance, outperforming rubber. With excellent load-bearing capacity and minimal deformation issues, it is a durable choice for various applications. Its exceptional impact resistance, wear properties, and elastic memory further enhance its appeal, making it an excellent option in many industrial settings.
-
How does PTFE Rod perform?PTFE products exhibit exceptional resistance to high and low temperatures, chemical reaction, corrosion, and stress-cracking. Its electrical and low-friction properties make it a preferred material for various applications.
-
Is PTFE Rod chemical resistant?PTFE is virtually inert against known elements and compounds, only attacked by alkaline metals in their elemental state, chlorine trifluoride, and elemental fluorine at high temperatures and pressures. It is insoluble in almost all solvents at temperatures up to about 300°C.
-
Is PTFE Rod wear resistant?PTFE Rod exhibits wear resistance depending on the severity of abrasiveness, speed, and loads. In some cases, wear resistance may be compromised if any of these factors are high. PTFE can be used as a filler to enhance the wear resistance of other materials and plastics.
-
Does PTFE Rod have a famous trade name?Yes, PTFE is famously known as Teflon® (DuPont).
-
What are the limitations of PTFE Rod?PTFE Rod is relatively soft, making it less suitable for certain high-stress applications. Additionally, it is more expensive than other plastics like nylon and acetal, and its relatively higher density makes it heavier than some other plastic options.
-
Can PTFE Rod be glued or bonded?PTFE must undergo surface preparation prior to bonding, using flame, corona discharge, plasma treatment, or etching. Various adhesives, including epoxies, polyurethanes, acrylics, and rubber-based adhesives, can be used. Some proprietary primers or specialist acrylic-based adhesives from companies like Loctite and 3M bond directly to PTFE without the need for extensive pre-treatment.
-
Why should you choose PTFE Rod?PTFE Rod offers an array of benefits, including high chemical resistance, excellent temperature capability, resistance to weathering, low friction, exceptional electrical and thermal insulation, and "slipperiness."
-
What are the typical applications of PTFE Rod?PTFE Rod is widely used in applications requiring sliding action of parts, such as plain bearings, gears, seals, cryogenic applications, and more. It excels in low friction applications, performing even better than nylon and acetal, and is comparable to ultra-high-molecular-weight polyethylene (UHMWPE) in wear resistance. Additionally, its high bulk resistivity makes it ideal for fabricating long-life electrets, the electrostatic analogues of magnets.
-
What is the size range, colours, and availability of PTFE Rod?PTFE Rod is available in white (natural) and diameters ranging from 4mm up to 120mm. For larger sizes, customers can contact our sales team for availability.
-
What are the unique characteristics of PTFE Rod?PTFE is the only known surface to which a gecko cannot stick.
-
What should be considered when using PTFE Rod?It is essential to avoid exposing PTFE Rod to temperatures above 400°C, as it can release highly toxic fumes of fluorides when heated to extreme temperatures. Proper safety measures should be followed during machining to prevent exposure to PTFE dust or shavings under such conditions.
-
What are the benefits of using PTFE Rod?PTFE Rod offers numerous advantages, including an incredibly low coefficient of friction, a maximum working temperature of +260°C (+300°C for short periods), exceptional electrical insulation properties, minimal moisture absorption, high chemical and acid resistance, and remarkable UV resistance. It is also one of the most thermally stable plastic materials, approved for food contact, and non-toxic.
-
What are the machining characteristics of PTFE Rod?Machining PTFE Rod can be challenging due to its softness, low friction, and "slipperiness." It requires a high-speed lathe with sharp tools and slow movement to prevent crushing or distortion. Swarf generated during machining can form long strings that may wrap around tooling.
-
What are the limitations of selecting Polyurethane Rod?Polyurethanes are generally not recommended for continuous hot water applications over 70°C.
-
Why choose Polyurethane Rod ?Polyurethane Rod is a versatile product, ideal for low-volume applications such as bump stops and bushings. It serves as an excellent replacement for rubber components that degrade over time, providing significant performance upgrades. With greater resistance to wear, it can outlast traditional materials by up to four times. Moreover, Polyurethane outperforms rubber in terms of resistance to permanent deformation, offering durability and preventing damage to associated components. Its high resistance to ageing, perishing, cutting with sharp edges, and impact further enhances its appeal.
-
What is the size range, colours, and availability of Polyurethane Rod?We stock Red 90 shore hardness in diameters: 12mm, 16mm, 20mm, 25mm, 38mm, 45mm, 50mm, and 63mm. However, other colours, shapes, and different shore harnesses are readily available from our sales team.
-
What commercial features does Polyurethane Rod possess?Polyurethane Rod stands out for its excellent abrasion resistance, exceptional low-temperature performance, and a combination of superior mechanical properties with rubber-like elasticity. It also boasts high shear strength, elasticity, and resistance to sunlight and weather conditions.
-
Does Polyurethane Rod have any unique characteristics?Among elastomers, polyurethanes boast the best resistance to gamma-ray radiation.
-
Is there a summary for Polyurethane Rod?Polyurethane Rod is a thermo-set plastic known for retaining its shape, flexibility, and resilience under stress, tension, or compression. Highly versatile, it can be formed into practically any shape, size, and hardness. Its superior abrasion, ageing, and tear resistance outperform rubber, while its excellent load-bearing capacity without deformation issues provides a durable solution. Compared to other plastics, Polyurethane Rod offers exceptional impact resistance, wear properties, and elastic memory, making it a reliable choice for various applications.
-
What should be considered when using Polyurethane Rod?Polyurethane Rod belongs to the category of thermo-set type engineering plastics, meaning it cannot be reheated and reformed like some other plastics.
-
What are the machining characteristics of Polyurethane Rod?Machining Polyurethane Rod to fine tolerances can be challenging. It requires razor-sharp high-speed steel cutters (not carbide), especially for 90-95A shore hardness. Softer varieties may prove nearly impossible to machine unless freezing the material is employed.
-
Is Polyurethane Rod wear resistant?Polyurethane Rod excels in applications with severe wear, such as on snow plough bases or vehicle suspension bushes. It often outperforms rubber, plastics, and metals in terms of abrasion resistance, allowing for fabrication of polyurethane products with less material compared to other materials.
-
What are the typical applications of Polyurethane Rod?Polyurethane Rod finds wide-ranging applications, including automotive suspension bushings, gaskets, seals, castors, wheels, bearing seals, valve inserts, shock absorbers, noise dampers, roller coaster and escalator wheels, as well as use as a wear strip on snow ploughs and pulleys on fishing trawlers.
-
Can Polyurethane Rod be glued and bonded?With proper preparation, Polyurethane Rod can be effectively bonded to metals and most plastics.
-
How does Polyurethane Rod perform?Polyurethane Rod exhibits a favourable temperature range from -32°C to 82°C. It excels in sound dampening, surpassing rubber, plastics, and metals in this regard. Furthermore, it demonstrates excellent electrical insulating properties.
-
Is Polyurethane Rod suitable for food applications?Polyurethane may be used as the surface layer in conveyor belts and in hose and tubing for conveying certain liquids.
-
What are the benefits of using Polyurethane Rod?Polyurethane Rod offers several advantages, including excellent abrasion resistance, resistance to oil and solvents, deformation resistance, resistance to ageing, tear resistance, and outstanding noise and vibration dampening properties. Additionally, it boasts a very good flex-life.
-
Is Polyurethane Rod chemical resistant?Polyurethane exhibits resistance to oil, grease, and solvents.
-
How long will Oilon Rod last?Customers have reported that Oilon Rod can last around four times longer than components made from black Nylon Rod, particularly in heavy-duty compacting machinery. After a trial batch, feedback indicated a significant performance improvement, leading to a complete switch to Oilon Rod for all rollers, as the cost was only slightly higher, but the performance gain was remarkable.
-
What is Oilon Rod?Oilon Rod is recognizable by its green colour, though the shade may vary depending on the manufacturer's focus on performance rather than cosmetic appearance. The unique attribute of Oilon Rod lies in its structure, containing an industrial, specially blended oil incorporated early in the manufacturing process. This oil-infused structure grants Oilon Rod exceptional wear resistance, reduced friction, and a much quieter operation.
-
How is Oilon Rod made?Oilon Rod is a Nylon 6 material with specially blended oil added to enhance its properties. It machines as easily as other Nylon Rods and is manufactured using the casting process, leading to lower internal stress than some extruded materials. This reduced stress ensures relative component stability and less distortion after machining. Oilon Rod is available in a similar size range to regular cast Nylon 6 Rod, making it easy to find the most economical size for specific applications. Direct Plastics has been a leading supplier of Oilon Rod for nearly two decades, maintaining a substantial stock of this key product at all times.
-
Is Oilon Rod quieter?Apart from its extended wear rates, another standout feature of Oilon Rod is its quiet operation. Items made from Oilon Rod produce minimal noise during service, making it an attractive selling point for various applications.
-
Is Oilon Rod more economical?While the initial investment in Oilon Rod may be slightly higher, it pays off over time by reducing ongoing maintenance costs. The inherent self-lubricating properties of Oilon Rod eliminate the need for regular maintenance, resulting in long-term cost savings.
-
How does Nylon 6.6 Rod differ from Nylon 6 Rod?Nylon 6.6 Rod is considered slightly harder and machines slightly better than Nylon 6 Rod, although the difference is not significant. The extrusion-only manufacturing process of Nylon 6.6 restricts its size range, particularly for larger sizes, as extruding large nylon rods is challenging for manufacturers.
-
Is Nylon 6.6 Sheet suitable for CNC Machines?Nylon 6.6 Rod is slightly better suited to automatic CNC machines than Nylon 6 Rod due to its slightly harder structure and higher temperature range. These properties result in less impact from heat build-up during the machining process, allowing for a slightly smoother finish.
-
Does Nylon 6.6 Rod absorb water?Nylon 6.6 Rod can absorb moisture (hydroscopic), potentially causing components with very tight and stable tolerances to vary if exposed to prolonged damp or wet environments.
-
What is Nylon 6.6 Rod?Nylon 6.6 Rod is the most widely used Nylon Rod in the UK, often specified in engineering drawings due to its ready availability and versatility in various applications.
-
What are the operating temperatures for Nylon 6.6 Rod?Nylon 6.6 Rod offers a slightly higher operating temperature range compared to Nylon 6 Rod, making it a better choice for components exposed to slightly elevated temperatures beyond the range of Nylon 6. Nylon 6.6 Rod is marginally more expensive due to the higher cost of the polymer from the producers.
-
Does black Nylon 6.6 Rod differ from natural?Black grades or charcoal grey versions of Nylon 6.6 Rod often contain an additive called Molybdenum disulphide (MoS2), acting as a self-lubricant and friction reducer. This makes black Nylon 6.6 Rod more durable and less prone to wear in industrial or abrasive environments.
-
Is Nylon 6.6 Rod suitable for food contact?The natural grade of Nylon 6.6 Rod is suitable for food contact, whereas the black grade, due to additives, should be reserved for industrial applications.
-
What are the applications of Polypropylene Rod?Polypropylene Rod is commonly used in acid or chemical components, thread protectors, and items requiring impact resistance.
-
What are the working temperatures of Polypropylene Rod?The maximum long-term working temperature for Polypropylene Rod is 80°C, which is lower than Nylon or Acetal.
-
Is Polypropylene Rod resistant to acids?Polypropylene Rod is highly resistant to acids, making it suitable for acid tanks and other chemical applications.
-
Is Polypropylene Rod economical?Polypropylene Rod is a cost-effective option, making it ideal for affordable or sacrificial components.
-
Is the weight of Polypropylene Rod considered light?Polypropylene Rod is extremely lightweight, even floating on water.
-
Could you tell me about the drawbacks of using Polypropylene Rods?Polypropylene Rod's machinability, working temperature, bonding, and fire resistance are some of its drawbacks.
-
What are the advantages of Polypropylene Rod?It offers excellent acid resistance but also chemical resistance. It is lightweight, non-stick and economical while it also offers impact resistance.
-
Is Polypropylene Rod fire resistant?Polypropylene Rod has a fire rating of HB, indicating that it burns and continues to burn even after the flame is removed.
-
Is Polypropylene Rod impact resistant?Polypropylene Rod has good impact resistance, making it suitable for components where impact is a factor.
-
Is the chemical resistance of Polypropylene Rod considered good?Polypropylene Rod offers excellent chemical resistance, making it suitable for chemical tanks and fittings.
-
Can Polypropylene Rod be bonded?Polypropylene Rod is difficult to bond effectively, but welding can be used as an alternative.
-
Is the adhesion of Polypropylene Rod low?Polypropylene exhibits low adhesion, making it advantageous in applications where materials should not stick to the component.
-
Can Polypropylene Rod be machined?Machining Polypropylene Rod requires caution due to its low melting point, and heat buildup must be avoided.
-
What are the drawbacks of Delrin Rod?Vulnerability to attacks by strong acids and oxidising agents Absence of ready availability in a flame-retardant grade Usual difficulty in bonding
-
What are Delrin Rod applications?Mechanical gears, slide-ways, and guiding elements Housing parts, screws, nuts, fan wheels, pump parts, valve bodies Electrical Engineering: insulators, bobbins, connectors, parts for electronic devices, etc. Vehicle: Fuel sender unit, Light stock (including shifter for light, turn signal), power windows, door lock systems, articulated shells Medical: insulin pen, Metered dose inhalers (MDI) Furniture: hardware, locks, handles, hinges Construction: Structural Glass - pod holder for point Packaging: aerosol cans, vehicle tanks
-
What is Delrin Rod?Delrin Rod, referred to as the "Homo-Polymer" grade of Acetal and bearing DuPont's trade name, offers exceptional load-bearing properties in both tension and compression. It exhibits minimal moisture absorption and resistance to a wide range of solvents. With a service temperature range of -29º to 85º C (intermittent at 93.3º C), Delrin Rod showcases high yield strength at elevated temperatures. Noteworthy features include low friction (highly slippery), superior wear resistance, and ease of fabrication.
-
Does Delrin Rod have other trade names?Ticona Hostaform, Celcon Pom H BASF Ultraform
-
What are Delrin Rod's machining characteristics?Delrin Rod proves excellent for machining using traditional methods such as turning, milling, and drilling. It leaves little or no burrs and requires sharp tools with a high clearance angle. Light clamping forces and sufficient workpiece support are necessary due to its lower rigidity than metals.
-
Why not choose Delrin Rod?While Delrin Rod has been approved for some food applications, it is not suitable for food storage due to its vulnerability to acidic foods.
-
What is Delrin Rod's chemical resistance?Delrin Rod may be sensitive to acid hydrolysis and oxidation by mineral acids and chlorine. In addition, it may experience susceptibility to alkaline attack and degradation in hot water. Low levels of chlorine in potable water supplies can lead to stress corrosion cracking, observed in both the USA and Europe in domestic and commercial water supply systems.
-
What is Delrin Rod's wear resistance?Delrin Rod combines lubricity and wear resistance, offering stiffness and strength in parts designed to replace most metal parts.
-
Why should you choose Delrin Rod?Delrin Rod presents a high performance, easily machinable engineering plastic, offering high strength, resistance to impact and fatigue, and excellent slipperiness. It proves more economical and easier to machine than most metals.
-
What are the benefits of Delrin Rod?Good mechanical strength Low coefficient of friction Effective heat resistance Good electrical and dielectric properties Low water absorption
-
Is Delrin Rod suitable for food applications?Delrin Rod can replace metal in automated food processing equipment, producing lighter, lower-cost, and corrosion-resistant components. Its low-friction properties are ideal for enhancing the speed of processing high-adhesion foods. It meets U.S. FDA standards, is USDA approved, and is not UV stabilised.
-
Is there a summary of Delrin Rod?Delrin Rod belongs to the Homo-Polymer grade of Acetal. While similar to the Copolymer grade, it excels in mechanical or strength applications. Both grades serve as engineering thermoplastics, ensuring precision parts with high stiffness, low friction, and exceptional dimensional stability. Widely used in automotive, consumer electronics, and industrial solutions, Delrin Rod finds applications in high-performance engineering components, making it a versatile and reliable choice.
-
What are Delrin Rod's size range, colours, and availability?Delrin Rod is naturally opaque white due to its high crystalline composition. It is also available in black, with rods offered in diameters ranging from 10mm to 200mm.
-
Can Delrin Rod be Glued and bonded?Delrin Rod typically poses challenges in bonding. Special processes like surface etching, flame treatment, or mechanical abrasion can improve bonding. Various adhesives, including epoxies, polyurethanes, and cyanoacrylates, can be used for bonding.
-
What is Delrin Rod used for?Delrin Rod finds typical applications in high performance engineering components such as gear wheels, ski bindings, fasteners, and crash pegs on motorcycles. It is also widely used in the automotive and consumer electronics industry.
-
How does Delrin Rod perform?Delrin Rod offers high tensile strength, stiffness, and creep resistance, outperforming many other polymers in impact resistance. It enables thinner and lighter part designs, displaying exceptional low and high-temperature performance, colorability, and favourable compatibility with metal and other polymers. Delrin Rod ensures dimensional stability in high precision moulding and allows for design flexibility.
-
What is Delrin Rod not suitable for?While Delrin Rod exhibits excellent resistance in areas requiring high wear, better materials like Nylon and UHMWPE exist for such applications. Additionally, in areas with strong chemical exposure, the Copolymer Acetal may be more suitable.
-
Is wear resistance good for PET Rod?PET Rod is known to outlast acetal in abrasive conditions and is as good as, if not better than, nylon in certain environments.
-
Is PET Rod known for having properties that reduce friction?PET Rod typically has low friction due to its hardness, leading it to be described as very slippery among engineering plastics.
-
How does PET Rod behave mechanically?The data sheet indicates that PET Rod is approximately 30% stronger than acetal and about 25% more rigid. It also has a better working temperature range and much lower expansion due to moisture absorption, around 60% better than even Acetal.
-
Can you provide a comparison between PET Rod and Acetal?PET Rod machines almost as well as Acetal, making it a practical option for various applications. It is over 30% stronger than Acetal and approximately 25% more rigid. PET Rod has a 10-degree advantage in short-term working temperature and a 30-degree advantage in long-term working temperature compared to Acetal. Additionally, PET Rod has a 25% lower thermal expansion rate and about 60% less moisture absorption. It exhibits a similar coefficient of friction and provides much better wear resistance. However, it is also approximately 40% more expensive than Acetal.
-
How does PET Rod compare to Nylon 66?PET Rod machines better than Nylon 66, delivering a similar or even better surface finish. It is 8% stronger and around 10% more rigid than Nylon 66. PET Rod has a 10-degree advantage in short-term working temperature and exhibits 50% lower thermal expansion rate. Remarkably, it has about 10 times less moisture absorption compared to Nylon 66 and offers a similar coefficient of friction and good wear resistance. However, it is approximately 50% more expensive than Nylon 66.
-
What are some drawbacks of PET Rod?At present, the size range for PET Rod is somewhat limited, with availability in only 10, 16, 20, 25, 30, 40, 50, and 60mm diameters. Additionally, its price is around 40% higher than acetal, and it is not suitable for applications involving hot water exceeding sixty degrees centigrade.
-
What is the suitability of PET Rod for machining?According to reports, PET Rod machines significantly better than Nylon and is comparable to Acetal in terms of machinability, making it a popular choice like Acetal.
-
Is PET Rod suitable for applications involving contact with food?Yes, PET Rod has FDA approval, making it compatible for use in food contact applications.
-
Can HDPE Rod be used for food applications?Yes, HDPE Rod is often used in the food production environment as the natural grade is food compatible. Its slightly waxy surface makes it difficult for food debris to adhere, making it suitable for applications like rolling pins.
-
What is HDPE Rod?HDPE Rod, or High Density Polyethylene Rod, has gained popularity as a general-purpose engineering plastic.
-
What are any disadvantages of HDPE Rod?There are however some, what some may describe as drawbacks which may or may not come into play for certain applications and one of them is the fact that HDPE Rod is very difficult to bond using adhesives. Although adhesive specialists advise us it can be bonded, they describe it as difficult at best and maybe the answer in this instance would be to weld HDPE using purpose designed welding equipment. A further drawback could be that it's not the hardest engineering plastic, it's not particularly soft but relative to some other plastics, HDPE Rod isn't the hardest. An indication would be that if you had strong nails and pressed really hard, you could cause a mark. The potential drawbacks could also be described as advantages in applications where the lack of adhesion is what’s required or where a component is required to be almost sacrificial as in the case of a drift.
-
Can HDPE Rod be used for food applications?HDPE Rod is often found in the food production environment as the natural grade is food compatible, it may be good for use as a rolling pin as food debris would find it difficult to adhere to the slightly waxy feel surface.
-
Is there a summary of HDPE Rod?So, if you're looking for a material that is economical, has low friction and good abrasion resistance, is also easy to machine but doesn't involve extreme loads or high impact resistance, then HDPE Rod would probably be worth investigating further. Please call or email our technical team if we can be of further assistance. Direct Plastics have a huge stock of the entire range of HDPE Rod and are set up to dispatch whatever engineering plastics you need immediately.
-
Is HDPE Rod an all-round performer?HDPE Rod may not excel in any single aspect, but it performs well in various applications, making it a versatile and strong performer overall.
-
Is there a summary of HDPE Rod?HDPE Rod is an economical, low-friction material with good abrasion resistance, easy machinability, and suitability for moderate loads and impact resistance. For applications that fit these criteria, HDPE Rod is worth further investigation. For immediate assistance, please contact our technical team at Direct Plastics, where we maintain a vast stock of the entire range of HDPE Rod and can dispatch the engineering plastics you need promptly.
-
Is HDPE Rod low friction?Yes, HDPE Rod exhibits low friction properties, making it advantageous for use in bearings or rollers. Additionally, HDPE Rod is lightweight and relatively inexpensive, providing cost-saving benefits.
-
What are any disadvantages of HDPE Rod?HDPE Rod has some potential drawbacks. It is challenging to bond using adhesives, although welding with purpose-designed equipment may provide an alternative solution. In terms of hardness, HDPE Rod is not the hardest among engineering plastics, but this can be advantageous in applications requiring lack of adhesion or sacrificial components, like drifts.
-
Is HDPE Rod suitable for wear resistance?HDPE Rod offers excellent wear and abrasion resistance, particularly in applications with moderate loads. When attempting to file HDPE Rod, even with relatively rough files, the material resists removal, showcasing its wear resistance.
-
What is Nylon 6 Rod?Nylon 6 Rod stands as one of the most favoured engineering plastics, recognized for its versatility and widespread use across various industries. Over the years, it has received multiple trade names from different companies, solidifying its reputation as a highly sought-after plastic.
-
What are the manufacturing processes for Nylon 6 Rod?There are two primary manufacturing processes for Nylon 6 Rod: extruded and cast. Extruded Nylon 6 Rod is produced by heating the polymer and forcing it through a circular die. On the other hand, cast Nylon 6 Rod is created by melting the polymer and pouring it into metal tubes that are capped at one end and open at the top.
-
Can I Drill Nylon 6 Rod?Drilling larger diameter cast Nylon 6 Rod must be approached with caution due to potential heat and vibration build-up. It requires very sharp drills and a gradual progression using incremental drill sizes until the desired size is achieved. Utilising coolant and a "pecking" action is essential. Using large blunt drills without considering heat or vibration build-up may cause the material to crack.
-
Does Nylon 6 Rod absorb water?All Nylon 6 Rods have the ability to absorb moisture, which may cause components to expand in damp environments. However, this is only significant if the finished components are exposed to operate under extremely tight tolerances.
-
What are the different types of Nylon 6 Rod?Both manufacturing processes have their advantages. Extruded Nylon 6 Rod is slightly cheaper and is available in diameters ranging from 6mm up to 300mm. Engineers have reported that it may seem softer and not as easy to machine, making it more susceptible to melting during machining. However, it benefits from a wider size range and lacks blow holes. Cast Nylon 6 Rod, on the other hand, is reportedly easier to machine due to less internal stress resulting from the manufacturing process. Although rare, it has a minute potential for blow holes and is generally perceived to be more stable with lower internal stress.
-
What are the main uses of Nylon 6 Rod?Nylon 6 Rod is commonly employed for pulleys, bearings, rollers, and gears, among other applications. It boasts exceptional strength, withstanding forces of up to 1 tonne per square inch, and exhibits high impact resistance, wear resistance, and low friction. If you seek an engineering plastic that excels in various applications, Nylon 6 Rod is likely the ideal material for your project.
-
What are the different colours and grades of Nylon 6 Rod?The majority of Nylon 6 Rod is manufactured in black or natural colours. Black Nylon 6 Rod, often containing an additive called Molybdenumdisylphide (MOS2), is preferred for industrial environments due to its self-lubricating graphite-type properties, providing extended longevity in wear or abrasive conditions.
-
What colours does Acetal Rod come in?Acetal Rod is primarily manufactured in Natural/White and Black colours, with Black being preferable for industrial applications. Additionally, we now offer blue Acetal Rod in stock, ensuring swift delivery for those with specific colour requirements.
-
Does Acetal Rod need less deburring?A significant advantage of Acetal Rod is its minimal generation of burrs after machining. This eliminates the need for time-consuming deburring processes, saving valuable time and resources.
-
What is the moisture absorption of Acetal Rod?One key advantage of Acetal Rod is its minimal moisture absorption, enabling precise machining and dimensional stability, regardless of environmental conditions. This characteristic makes it an ideal choice for components expected to function in damp or wet environments.
-
Is Acetal Rod suitable for food applications?Yes, Acetal Rod is an excellent choice for applications involving food. Its minimal moisture absorption ensures food safety by preventing bacteria absorption. Many companies in the food industry specifically request components machined from Acetal, and this is why we maintain a stock of Blue Acetal Rod. The blue colour facilitates easy visual inspection, simplifying the detection of debris without affecting the entire batch.
-
Is Acetal suitable for CNC Machines?Acetal Rod demonstrates excellent compatibility with high-speed automated machining processes like CNC lathes. This allows for efficient, automated production, significantly reducing manual labour while producing finely machined parts.
-
Is Acetal Rod slippery?Indeed, Acetal Rod is well-known for its slippery nature. This attribute imparts low friction characteristics to components and minimises initial stickiness. For small rotating components that require smooth initiation during service, Acetal provides an advantage by not requiring significant initial load, thus reducing jerking, which can be a real concern, especially in micro components.
-
Does Acetal Sheet absorb less moisture?Yes, Acetal Sheet exhibits minimal moisture absorption, ensuring dimensional stability during machining, storage, and actual use. This characteristic makes it particularly suitable for marine applications and environments with high humidity.
-
What is an Acetal Sheet?Acetal Sheet is a top engineering plastic for machining, chipping efficiently during the process, resulting in an outstanding surface finish with minimal visible marks. Its nearly burr-free finish is advantageous for intricate parts, eliminating the need for manual deburring.
-
Is Acetal Sheet suitable for Food use?Acetal Sheet is highly sought after in food preparation and production industries due to its food contact safe properties, non-toxicity, and resistance to bacterial formation.
-
Is Acetal Sheet low in friction?Indeed, Acetal Sheet offers low friction characteristics, making it ideal for sliding components and delicate instruments that require smooth operation.
-
Is Acetal Sheet suitable for CNC Machines?Acetal Sheet is an excellent choice for high-speed CNC automated machines, requiring minimal intervention during the machining process.
-
What is the availability of Acetal Sheets?Currently, Acetal Sheet is predominantly available in black or white/natural colours. Consideration is given to introducing blue Acetal Sheet, especially useful for food production companies as it allows easy detection of potential debris during inspections, reducing the likelihood of contamination hazards.
bottom of page